“EPIQ Mecfor Casthouse Solution brings the right solutions by considering the holistic and long-term success of the cast house”
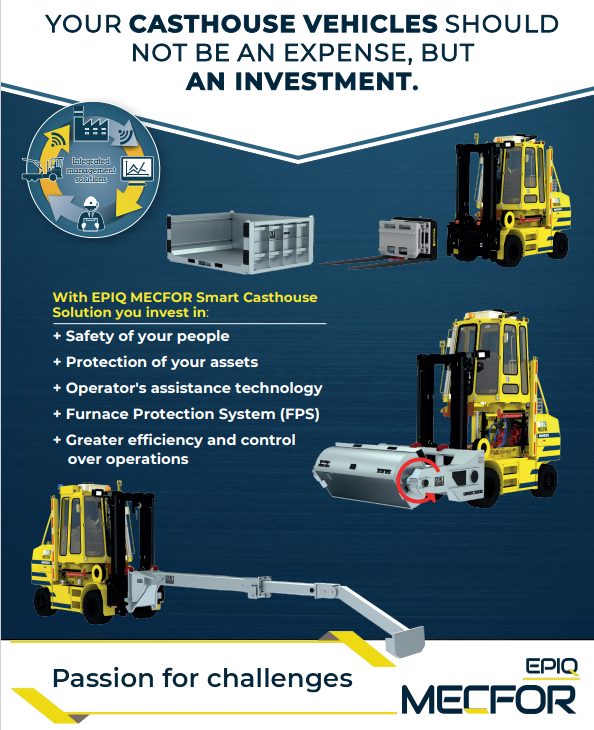
EPIQ Machinery is a world leader in heavy equipment for the aluminium, pulp and paper, and rail equipment industries. The company has diversified activities on various niche markets providing a solid installed base and a strong capacity for its aftermarket services. All at EPIQ share the same passion for challenges. The growth is based on deeply embedded values with active listening and the capacity to adapt the offer for greater flexibility.
It was a great opportunity for AlCircle to get an interview with the top executives of EPIQ Mecfor.
Yannick Beaulé, Chief Revenue Officer
Kevin Williams, General Sales Manager – Primary Metals
Marty De Goey, Business Development / Application Specialist – Primary Metals
Isabelle Gaudreau, Marketing and Communication Coordinator
AlCircle: What new opportunities do you expect in the Global Aluminium Foundry industry in 2022 and beyond?
EPIQ Mecfor: As we all recover from the COVID crisis, one of the biggest challenges for the industry may simply be to respond to market growth. Aluminium’s increasing consumption is being driven by its unique properties. Over the last decade, automotive and aerospace have developed and implemented many innovative uses for aluminium alloys. Nowadays, electrical engineering brings up new openings and opportunities. Because the material is non-magnetic and ductile, it tends to solve many design issues for the electric vehicle market among others.
Being endlessly recyclable, aluminium shows many advantages: sustainable development, corrosion resistance, a good conductor of electricity and lightweight material. No wonder why the industry has been so active over the last years. Moreover, the Secondary (recycled) Aluminium sector has gone through many changes: environmental craze that pushed up demand for recycled aluminium combined with a wider variety of alloys available for automotive, aeronautic and construction applications.
To navigate through these changes, the industry players are showing greater safety awareness over the complete production process. In addition, energy savings and environmental footprint could very well be their next priority. In a near future, more stringent environmental standards will be requested in an effort for decarbonization to reach zero emission (or almost).
AlCircle: What according to you are the most common challenges faced by aluminium foundries across the world? How to overcome those challenges to make the industry sustainable?
EPIQ Mecfor: Safety and Energy savings are at the core of the decision-making process. While Primary Aluminium foundries look into loading bigger batches into the melting furnace; Secondary foundries are investigating ways to improve the management of recycled waste. The industry will also need to find ways to cope with a shortage of personnel as well as structural supply chain issues.
To overcome these challenges, we, at EPIQ Machinery, are improving our Smart Casthouse solution by introducing a new vehicle called EPIQ Mecfor Furnace Vehicle (MFV) and by increasing embedded technologies onto our equipment. Our Smart solution helps facilities understand the equipment usage, can schedule maintenance time, tool usage and consumption rates, and added personnel safety in and out of the equipment. These are just a few of the benefits our customers are seeing, and this helps generate more profitability for the end-user.
Material handling is sometimes an afterthought, especially after expansions or increases in demand. At EPIQ Machinery we like to take the approach that we want to understand your current operation and possible plans for the future. We know not all plants stay making the same product for their lifespan. We look at how we can make the material handling and process flow work for the current needs and possible expansions or upgrades.
AlCircle: Can you elaborate with details about the EPIQ Mecfor smart casthouse solution? Why do you think your vehicle is the best in the industry?
EPIQ Mecfor : Over decades, EPIQ Mecfor has perfected its Smart Casthouse Solution offer. The Multipurpose Casthouse Vehicle (MVR) or the EPIQ Mecfor Furnace Vehicle (MFV) can be coupled to QuicKonnect tools. To date, EPIQ MECFOR has a portfolio of over 525 different tools designed, built, and in operation. Also, furnace tending is made easier; thanks to the choice of over 64 blade designs available to fit all furnace configurations.
EPIQ Mecfor Casthouse Solution brings the right solutions by considering the holistic and long-term success of the cast house. It bridges that gap between safety and efficiency. Anyone working in or around cast houses is aware of the dangers. The understanding of the value that derives from safe and risk-free operational environments is tremendous.
Advances in safety to further reduce injury rates (and thus reducing the applicable costs to employers) must come through true innovation, such as equipment and tool specialization that simultaneously diminishes risks of bad practices, clutter and coactivity. Safety must be fundamentally built into cast house operations as strategically as the smelting processes themselves. A smart multipurpose-built vehicle that bridges the gap between efficient and safe operations– one that manages to boost the bottom line while protecting the frontline. An exclusive vehicle that moves current process industry prerogatives closer to their objectives.
Finally, the merge between MECFOR and AD to create EPIQ Machinery opens to customers unique niche expertise in the supply of mobile and ground-based automation equipment. We understand that ROI is the key; we’ve started to pool our talents and specialities for better and greater integrated cast house equipment from furnace loading, tending, and cleaning up to more sophisticated casting lines and handling of finished products.
AlCircle: What new technologies do you think will play an important role in aluminium foundries in 2022?
EPIQ Mecfor: Electrification and robotization, new technologies that will help aluminium producers reduce their carbon footprint. EPIQ Machinery is actively working on its fully electric Automated Guided Vehicle (AGV) and looking into broadening EPIQ’s offer.
Also, as a FANUC robot integrator, EPIQ Machinery can integrate more automation in the process, especially for the casting line.
AlCircle: What new technologies are you planning to introduce to your foundries this year?
EPIQ Mecfor: To name a few, the next year will be to perfect our Furnace Protection System (FPS), SmartConnect and MECFORLink; one of our most recent innovations offered to cast house customers.
Always being in an R&D mode, EPIQ Machinery is open to working in cooperation with customers to design better-suited tools to meet current needs. Recently, our team has developed: conveyor type forks to manipulate bigger ingots; QuickConnect Ecumax, bin tilter, extra capacity loading bins, to name a few. We also have an AGV for crucible hauling in the smelter that is potroom rated and is completing a set of trials.
AlCircle: Do you think Industry 4.0 will become an integral part of the global aluminium foundry industry in years to come?
EPIQ Mecfor: At EPIQ Machinery, we think that Industry 4.0 opens numerous possibilities and that it inevitably permeates our lives. Technologies are rapidly evolving and becoming more accessible with user-friendly intuitive interfaces. Our goal is to deliver fully integrated equipment with embedded technologies, some standard features while others can be offered in options.
However, it is crucial to understand that to benefit from all the advantages of Industry 4.0 there will need to be a change in the relationship between manufacturer and foundries, driven by the integration aspect of all technologies and the important point of IT infrastructure safety.
AlCircle: What according to you will be the key industrial sectors that will drive the global aluminium foundry business this year?
EPIQ Mecfor: In Quebec, under the ‘Aluminium Valley Society’ cluster, organizations are working to develop new markets to find more uses for aluminium in our day-to-day. The rise of electric vehicles on the consumer market and among industrials will bring new needs. We also know that automotive parts, sheet, and body production are growing as more manufacturers look for lightweight alternatives. UBC recycling should see an increase as recyclers and remelters look for post-consumer materials that they can remelt in their casting process.
As a leader in the aluminium sector for material handling and mobile equipment, we know that there will be more cooperation between suppliers. As we set the route for the future of aluminium, some challenges require pooling specific expertise developed by more than one company. Thus, this desire to better cooperate is based on openness, respect, and the achievement of mutual objectives. This will allow the emergence of efficient and innovative machines to better fit the needs of end-users. In these situations, the challenge lies in identifying the right partners with whom we will be able to walk this path, beyond any doubt, with shared reassurance and sound business ethics.
Source: AlCircle.com / E-magazine: Global Aluminium Foundry: Challenges and Opportunities ahead 2022