Recycling: the challenges of managing aluminium scrap in secondary production smelter
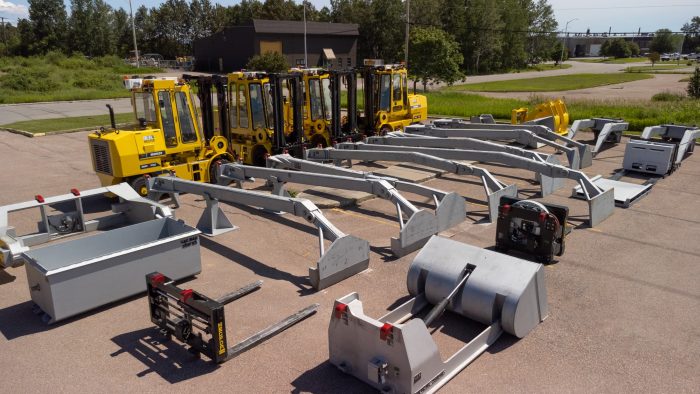
What makes EPIQ Machinery stands out from others in the aluminium scrap handling in secondary production sector?
Even before recycling became in vogue and that versatility and multiple uses of aluminium was found applicable in a variety of sectors, under the MECFOR brand, EPIQ supported its secondary plant producers to optimize their operations. For many years, secondary facilities have been the poor children of industry. To ensure their profitability, it became imperative to have a high-yield pragmatic approach.
This is how the ‘Smart Casthouse’ solution took off and is now experiencing great enthusiasm for both secondary and primary facilities. Not only for the optimization of the fleet of vehicles needed to perform many tasks in a foundry, but especially for the new operator assistance functions thanks to the ‘Smart Connect’ technology developed by the MECFOR engineering team.
Nowadays, producers are exploring the notion of circular economy by rethinking their production methods such as closed loop recycling. EPIQ has many customers now that are looking at setting up facilities that include their own scrap metal recycling facilities. This ensure a good supply of recycled aluminium for re-melt.
With our AD brand, our sawing and packaging systems make the recovery of cutting chips and the management of non-compliant billets facilitated by a fully automated process. This allows the producers better handling options for the remelting of this material into the best possible alloy. Therefore, AD’s expertise in inspection, precision of cuts, batching of billets allowing efficient sorting of finished products combined with that of MECFOR Smart Casthouse mobile equipment, it allows our customer the ability to manage scrap efficiently and safely.
Although, we are not remelting specialist or involved in the recycling process. Due to our expertise in up-to-date modern materials handling solutions, we can optimize the charging and management of your furnace, utilizing methods that will in turn offer overall gains. Our solutions make your process safer, go faster, using energy efficient methods with minimal auxiliary negative impact.
Challenges and Solutions: how does EPIQ Machinery address real-life situations and overcome major obstacles during the recycling process?
We’ve noticed that the remelting furnaces are getting bigger and that our customers are looking to load more to also reduce the number of times they need to open the furnace doors. It is in this state of mind, that our team developed the ‘MECFOR Furnace Vehicle Telehandler – MFV’. This equipment has a totally new design offering a cab elevation system, telescopic boom, front free wheeled axle, rear steering axle and high lifting capacity. The new MFV is compatible with MECFOR Smart Casthouse technologies using the QuicKonnect system, Operator’s assistance technology and Furnace Protection System (FPS). The MFV allows to pre-charged large boxes with scrap.
Adding to the mobile machine described above we can add to the overall solution the AD rail bound charge machine. These machines are capable of loading up to 40,000 lbs of scrap or prime material in one push. As well, they reduce the door open time thus improving the melt rates and reduce heat loss. Like the tending machines, they can be tied to a camera system. Looking into the furnace during the melting cycle to best determine when they need to charge or tend the furnace.
Innovative technologies offered by EPIQ Machinery utilized in aluminium recycling processes. How do these technologies contribute to increased efficiency and sustainability?
Our AD brand has an automatic rotary furnace charge machine. Much like our machine for the larger remelt furnaces this car is design specifically for rotary furnaces. Rotary furnaces are used to re-process scrap material and dross generated by the typical remelt furnace. These charge machines can operate automatically once loaded with the charge material. Not only does it improve the turn around time for charge but greatly reduces the damage to the refractory ring at the furnace opening generally cause my large lift truck loading practices.
How do you maintain a circular economy in your operations? What is your insight on closed loop recycling system?
At our facilities, we have processes in place to recycle scraps from our manufacturing activities. Each of our employees is aware of reducing their carbon footprint as much as possible.
Of all your existing material holders, which according to you will be in demand this year?
What we hear from the market are greater interests of process automation. That includes Auto Guided Vehicle (AGV) and Autonomous Mobile Robots (AMR) solutions. Being a company that blurs the line between a technology company and a heavy machinery manufacturer, we continuously seeking for innovative way to meet the challenges of our customers. This is why we now have this type of equipment available under EPIQ DTA brand. If we look further ahead, we foresee that hyper-connectivity and a systematic approach between all equipment fixed and mobile operating in a smelter will become the next step.
Finally, electrification of mobile equipment offering is also the talk of the town. All industry players are geared towards achieving the carbon neutral objective. As a supplier close to its customers, we stand by them and are working on heavy-duty mobile equipment with fully electric motorisation type. We are also looking at electrifying more of our material handling solutions where you would typically see a hydraulic solution. This allows facilities to operate cleaner without having hydraulic leaks contaminate the surrounding area.
Authors
Marty De Goey, Application Specialist
Isabelle Gaudreau, Marketing and Communication Coordinator