Reinventing intelligent equipment through autonomy and innovation: EPIQ Machinery shares its vision with AL Circle
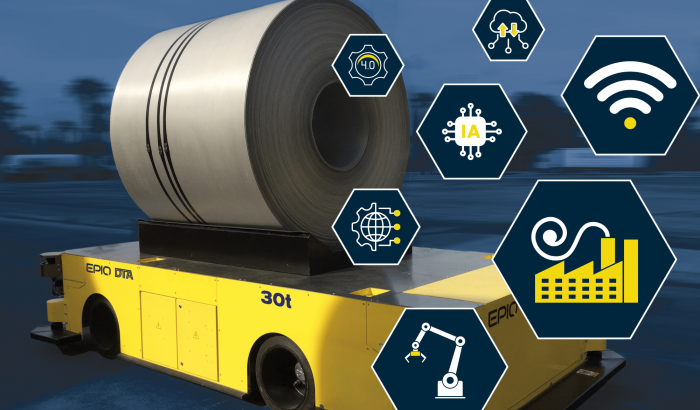
To bring its equipment solutions from ‘smart’ to ‘intelligent’, EPIQ envisions for a near future to connect Manufacturing Execution System (MES) and Manufacturing Operations Management (MOM) technologies to its equipment.
1. Beyond Smart: How is EPIQ Machinery redefining the concept of “intelligent” equipment in aluminium production through AI, edge computing, and real-time data autonomy? Are we approaching a point where predictive systems can independently drive process optimisation?
Being a designer and equipment manufacturer, EPIQ is well positioned to implement a broader vision and definition of tomorrow’s equipment suppliers’ role. With years of experience, the EPIQ group professionals are aware of the operational reality and understands the constraints of cost control of its customers while having to always beat production quotas.
We are all witnessing a transformation of heavy industrial material handling through Industry 4.0 capabilities, combining automation, robotics, and digitalization to deliver intelligent, end-to-end solutions. Our ambitious goal is to offer fully integrated systems that connect multiple products, with complete digital ecosystem solutions. Having this ability is a real competitive edge allowing our engineering to think and plan ahead on how to integrate technologies.
We believe that the gap between ‘smart’ and ‘intelligent’ lies in the fact that beyond collecting data that allows our engineers to improve ‘fail safe’ type of equipment behaviours (smart); the machine will interact with the complete process and will adapt/prioritize a set of operations based on the convergence of the system data analysis results (intelligent).
For example, EPIQ Digital team is developing a Production Management software application (e.g.: InNexus™). In turn, EPIQ Machinery line of product engineers can integrate, onto our handling equipment, tools and artificial intelligence (IA) solutions compatible with the software ensuring a smooth interface and integration of interconnected equipment solutions that will now:
- Create a unified data ecosystem that enables seamless coordination, real-time status updates, and autonomous task allocation.
- Drive self-optimization of operations by learning from operational data, continuously improving efficiency, safety, and resource utilization.
- Predict autonomously handling needs from raw material handling, to carbon plant, electrolysis sector, casthouse up to warehousing of finished products.
As an example, over the last 10 years, EPIQ has offered its Smart Casthouse Solution under its MECFOR line of products. This solution streamlines the number of vehicles required to execute furnace operations. The ‘smart’ aspect is that once a specific specialized tool is connected, the MVR vehicle recognizes the tool and its function. Once the vehicle is in position in front of the furnace, the operator launches the program associated with the tool. The program deploys the right automated movement sequences that offer optimum results within the dimensional parameters of the furnace. This ‘smart’ solution allows for safety of operators and efficiency of operations.
To bring the solution from ‘smart’ to ‘intelligent’, EPIQ can envision a technology that will support the production management program connected to the MVR vehicles. It may be that instead of loading the furnace with more material, the MOM will send information to adjust the furnace temperature and ask to connect to a stirring blade because it has received a signal that the batch was not dissolving properly. And before loading with more material, the molten metal must be stirred once more.
Therefore, EPIQ will not solely deliver an equipment but rather an ecosystem that will autonomously navigate, manipulate, and coordinate material flow with adaptive, predictive decision-making, enhancing safety, efficiency, and flexibility across the production lifecycle, while lowering maintenance costs.
And yes, the industry is approaching a point where predictive system can drive optimisation.
2. With sustainability at the core of industrial agendas, how does EPIQ Machinery approach lifecycle sustainability for its heavy equipment—from design to end-of-life recycling—especially in energy-intensive operations like anode production and casting centres?
Sustainability starts in our own facilities, in our own process to minimize impact of the whole supply chain. We, at EPIQ, favour a conscious use of resources such as water, power supplies and raw materials. In our business, we build our machine using robust steel and we are enforcing local recycling of steel scrap generated by our manufacturing processes.
We strongly believe that sustainability is both our responsibility and a necessity. It is embedded into the lifecycle of all EPIQ Machinery systems supplied to our customers. It basically starts with the design of the machine pneumatic, hydraulic, and smart automation systems. The systems are not over-designed and are programmed in such a way as to make sure that the machine conserves energy by operating only when needed, with precisely calibrated cycles that minimize movements within optimal limits, eliminating wasteful operations.
Furthermore, EPIQ supports its equipment from delivery and all over the lifecycle of the equipment. Having a close to customer approach, our team works together to make sure that installed based equipment work at its best. Our sales representatives have an in-depth understanding of our equipment staying in touch with our customers. Plus, our qualified aftersales technicians can offer audit and/or refurbished program to make sure that the equipment remain efficient by updating with automation and/or high-performance components.
3. How is EPIQ Machinery navigating the increasing convergence of cybersecurity and industrial automation, particularly in aluminium smelting operations where operational technology (OT) is increasingly connected to enterprise IT and cloud platforms?
As we evolve from being solely an?Original?Equipment?Manufacturer toward a truly Intelligent Manufacturing partner, we must advance in lock?step with cutting?edge technology.?Buzz?terms such as cybersecurity, big data, IT?OT convergence, and cloud platforms are everywhere, yet it all still begins on Level?0—the field sensors—and rises through the control layer?(PLC,?DCS,?HMI,?SCADA). When you are orchestrating plant?wide aluminium?smelting operations, the network becomes the plant’s nervous system.
Linking that nervous system to MES/MOM as InNexus™ is now essential for sharper manufacturing objectives: lower losses, faster time?to?market, and higher productivity.?That makes secure IT?OT convergence non?negotiable.
At?EPIQ?Machinery we put cybersecurity at the core of every convergence project. For aluminium?smelting sites, we begin with a rigorous OT?network assessment: vulnerability scanning, topology mapping, and physical?infrastructure inspections. We then review and harden security policies, ensuring that each layer from sensor to cloud meets both operational and enterprise standards
4. Can you share insights into the most complex system integration project EPIQ has recently executed for the aluminium sector—what made it unique, and how did it challenge conventional engineering or automation approaches?
A recent project is for an Anode Slot Cutting Machine, which represents one of the most complex system integration efforts by EPIQ Machinery. It involves handling anodes that weigh several tonnes, and managing such a system demands a high level of precision and strict safety measures.
Traditionally, we used to write simulation logic directly in the PLC to test various conditions and analyse system operation, ensuring all safety interlocks were in place. However, such methods have limitations—you can’t simulate physical behaviours or accurately predict how the system will respond when it’s carrying heavy loads.
To overcome these challenges, all our EPIQ Machinery projects now go through Simulation & Virtual Commissioning (Digital Twin). By testing the control system with a simulated model, our engineers gain a much deeper understanding of the complete control logic and safety mechanisms. It also allows us to explore various scenarios that wouldn’t be possible or safe to test on the physical system.
5. As workforce demographics shift and skilled labour shortages persist, how is EPIQ incorporating human-machine collaboration, augmented reality (AR), or remote assistive technologies into its material handling systems to future-proof aluminium operations?
We understand very well that equipment failure can cause a production bottleneck. For years, EPIQ has been offering remote technical assistance to its customers. That with the focus of maintaining the right process flow and minimizing downtime. Our goal is to ensure that breakage does not occur or occurs as little and for as short a time as possible. No matter where our customers are; EPIQ will be available and provide the required assistance.
On another note, with demographic shifts and the persistent challenge of finding skilled labour, it’s clear that we can’t avoid the situation—but there is always an opportunity to make things better, safer, and more optimized through innovative solutions.
For example, we are introducing Virtual Reality (VR) into our simulated machine models and incorporating training modules that allow operators to get a real feel for the machine before they physically operate it.
Additionally, we are implementing industrial automation solutions capable of handling large-scale and repetitive tasks, while maintaining safety as our highest priority. The automation, combined with AGV/AMR systems, significantly reduces the risk associated with moving heavy loads from one place to another. This not only lessens dependence on manual labour but also minimizes the hazards involved in material handling.
6. Given the emerging importance of low-carbon aluminium certifications and ESG-linked reporting, how are EPIQ’s automation and digital platforms assisting producers in real-time traceability, emissions accounting, and transparent sustainability disclosures?
At EPIQ, we recognize that sustainability is no longer optional—it’s now a core metric of operational excellence. With growing emphasis on low-carbon aluminium certifications and ESG-linked reporting, producers need systems that provide real-time visibility, traceability, and verifiable data across the full production chain.
Our answer to this challenge is InNexus™, EPIQ’s intelligent manufacturing operations platform. InNexus™ functions as the brain of the aluminium production process—seamlessly connecting production equipment, data sources, and control systems into a unified digital ecosystem—providing live dashboards that track energy use, CO? emissions, and process KPIs at every step of the value chain. This supports immediate corrective action and enables producers to generate auditable records for ESG disclosures and low-carbon certifications such as ASI, ISO 14064, or GHG Protocol.
Another example is with EPIQ’s ability to integrate SERMA (Specific Electrical Resistance Measurement of Anodes)—a non-destructive, real-time quality control system developed by our partner Dynamic Concept. SERMA detects internal defects in both green and baked anodes using electrical resistivity mapping. By identifying underperforming anodes early, producers can avoid sending poor-quality material to the potroom, reducing energy waste, preventing double work, and cutting carbon emissions, all of which translate into measurable OPEX savings and sustainability gains.
By combining intelligent equipment (like our world-renowned anode slot cutting machines), real-time anode screening via SERMA, and centralized digital infrastructure through InNexus™, EPIQ enables aluminium producers to shift from reactive compliance to proactive, data-driven sustainability. This is not just about improving the process—it’s about securing a future-ready, low-carbon aluminium operation with full traceability, accountability, and Operational performance optimization built in.
7. Looking to 2030, what disruptive force—whether technological, regulatory, or geopolitical—does EPIQ Machinery believe will most significantly reshape the aluminium production value chain, and how is your innovation roadmap preparing for it today?
We believe that the digitalization shift will have the most impact on the global heavy-duty handling industry. As we enter a new industrial era driven by technological breakthroughs, EPIQ’s innovation roadmap is set around automation, robotization and digitalization.
By allowing our equipment to think and communicate, we will empower our customers to answer the challenges of decarbonation, while succeeding in a very competitive environment.
This means designing fully integrated material handling systems with world-class heavy-duty equipment, instrumented with control systems capturing live information that can be leveraged optimally with an updated MES/MOM software.
AUTHORS
Member of EPIQ’s executive team, Yannick Beaulé holds the position of Chief Revenue Officer at EPIQ Machinery since August 2021. His diversified experience in key positions related to sales, but also to operations and general management of companies working in the sale of equipment and technical solutions for heavy industrial customers, is a major asset.
He has experience managing companies with multi-site teams, opened service centers, integrated and developed new products and markets, negotiated partnership agreements and contracts with major clients.
Rupali Kaushik Heads the Services and Marketing at NOVIMEQ Automation by EPIQ and leads the efforts on Global Marketing & Business Development of Automation Services, with a focus on building a strong service marketplace in industrial automation.
With a career that began in 2006, Rupali brings deep expertise from her work in automation across multiple industries. Her background in engineering, marketing, and entrepreneurship gives her a unique perspective on industry needs, technical innovation, and customer-focused solutions.
This article was featured in the Advanced Industrial Technologies in the ALuminium Industry (Part II) edition (Vol. 32, Juin 2025) of the e-Magazine AL Circle, on pages 8-17