Staying a Step Ahead of Customer Needs
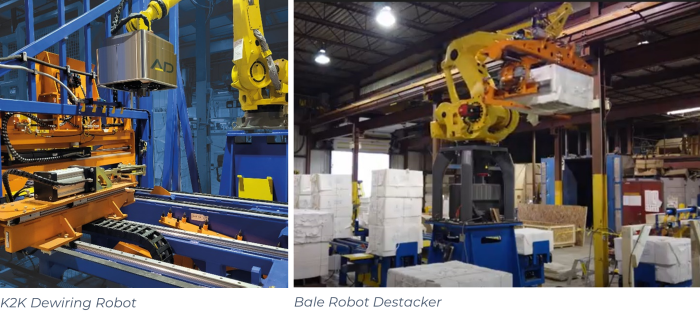
Formed in 2021 as a result of a merger between Mecfor and Advanced Dynamics, Quebec-based EPIQ Machinery specializes in the handling and conveyance of pulp bales, including feed systems and warehousing.
Although this may seem like a straightforward step in the overall papermaking process, increasingly complex paper “recipes” calling for a number of different pulps make this an area where advanced automation technology, particularly robotics, can increase efficiency and productivity while vastly decreasing the safety risks involved, i.e., dewiring.
EPIQ’s Peter Hanna, Director – North American Regional Sales, cited one North American tissue mill, built in the mid-1960s., producing 150-200 tons/day. Looking to expand its product range and increase production as far back as 2010, the mill knew it needed to greatly expand its pulp feeder system to five species in five stack lanes. For various reasons, many technological, the project was pushed back. The project was completed in 2018, taking one year from order to engineering to start-up.
Bales Destacking zone – five species, five lanes
In the intervening years, the evolution of the technology starting with dewiring of pulp bales. One of the most hazardous jobs in a mill, automatic dewiring technology was introduced in the mid-1980s with EPIQ (its predecessor companies) at the forefront.
Although an important safety measure, automatic dewiring took a person away from the direct flow of pulp infeed. So, a metal sensor was needed to ensure no rogue metal fell into the pulper. If metal was detected, the pulp bale was rejected.
But, Hanna notes, if a bale is rejected, it needs to be made up to ensure the batch size and recipe is correct. And, swinging between pulp species further complicated the reject-refeed process. In most tissue mills, pulp blending happens frequently. This led to the development of robotic destacking in the last five years.
Hanna further explains that pulp is usually stacked six bales high, but if the recipe calls for nine bales of a particular pulp, the destacker needs to take six bales from one stack and three from another. “The robot can pick off the top of any stack. It is very unique. It makes for a much more efficient process.”
Automatic dewiring, metal detection, blending softwood and hardwood pulps, new recipes have all led to a new era of pulp infeed systems.
EPIQ’s client, a non-integrated facility, was looking to run five different pulp species into three pulpers. Therefore, EPIQ’s first robotic destacker was installed in the mill. “The destacker was a game changer,” Hanna says.
Wire ball from dewiring robot operation
In the end, EPIQ’s scope of supply included five stack infeed systems, Fanuc robots, and MDI metal detector, Rockwell control system (in Europe, EPIQ uses Siemens) all feeding three batch pulper conveyors. Wires removed by the robot are automatically compacted in a large wire baller, for easy recycling.
The mill had a simple process that with an increase in production and new products became more complex. This is a challenge that many mills face. But, as the pulp infeed process becomes more complex, the equipment needed to run the system also becomes more sophisticated. So how to service?
Hanna says that any robotic system EPIQ installs will be fully supported by its trained technicians. They work with the mill’s E&I personnel who are responsible for operations in the mill. “We train the E&I people. We can provide service remotely or on site.”
He adds that 98% of calls from the field are handled over the phone.
Up until the 1990s, robots in the pulp infeed process were not common. So, mills were hesitant to install them. As they became more common, especially in roll wrapping, and converting the concept of expanding their use to other parts of the plant were not so much a concern.
And, Hanna says that younger generation are excited about working with robots, even from their phones. They have robotic education from their school days and want to use it. They are comfortable with new technology.
In North America particularly, there are many older mills running. Space can be at a premium. Process flows can often be convoluted. Hanna admits it can sometimes be a challenge but says that robots now can “work around corner or up against a column. We can program robots to work in extremely tight places.”
EPIQ is now working with a client with six small remote pulpers spread across a mill. It is looking at one satellite dewiring system, with wire-free bales then re-stacked two high and sent to the pulpers on an AGV (no fork trucks).
There are capital costs involved with any new technology, but compared with the way mills used the handle the infeed process, safety and production improve. Generally, not more than one dewiring robot will be needed in a typical system. Also, with a much lower chance of metal contamination, pulpers will need less maintenance.
Working globally, the company is active in many industries, primarily pulp and paper and primary metals. Besides it pulp infeed systems, EPIQ also can supply warehousing, roll handling and wrapping processes.
Pulp infeed line conveyors
The company promotes the EPIQ Way. Isabelle Gaudreau, Marketing & Communications Coordinator, explains it as the company striving to be one step ahead of its customers’ needs, to foresee customer issues and ensure EPIQ’s equipment works as it should. And, that EPIQ’s equipment integrates with its customers’ other process equipment. “We will never let our customers down. We will be there to solve any issues that arise.”
BOXED COPY SIDEBAR
Wire vs wireless
Although there have been efforts made to eliminate wires from pulp bales, it is still the main method to secure bales.
Repulpable strapping and glued bales have been introduced, but Hanna says wires is still the primary method of securing dried pulp bales for shipment. “Wire has stayed because it provides package strength for just about any type of bale or stack handling. Today, we see about a 75:25 split.
“Our systems sense for wire and they are smart enough to sense when a bale is wireless and pass them on through”
He adds that repulpable straps can be tougher to slush and if the bale doesn’t break apart in the pulper, it can be tough on the rotor. “We do have a pulp strap cutter for this situation.”
FOR INFORMATION
Peter Hanna, Regional Sales Director – North America